At JLYPT, we specialise in high-performance PVD (Physical Vapor Deposition) coating services for industries that demand precision, durability, and surface excellence. PVD is a vacuum-based thin film process where solid materials are vaporized and deposited atom-by-atom, creating ultra-hard, wear-resistant, and chemically stable coatings.
Our advanced capabilities include both sputtering and thermal evaporation methods, enabling us to tailor coatings for a wide range of applications—from optical components and medical devices to aerospace and decorative finishes. With tight control over coating thickness and uniformity, JLYPT ensures each part meets the highest standards of quality without compromising dimensional accuracy.
Advantages Of PVD Coating
PVD coating is an alternative to traditional metal coating processes, where a thin layer of metal coats a substrate. In industry, metal coating processes use either an electric current (electroplating) or an autocatalytic process (electroless plating) to achieve a strong bond between the substrate and metal. However, many traditional coating processes also produce potentially harmful waste products, and some processes such as cadmium coating are decreasing in popularity due to safety concerns.
PVD coating requires no compounds other than the substrate and target material, resulting in a more environmentally friendly, safe process that caters to a wide range of industries and applications.
PVD coatings offer exceptional durability, forming a hard, dense surface layer that resists wear, corrosion, and oxidation even under extreme conditions. Unlike traditional coatings, PVD bonds at the atomic level, ensuring long-lasting protection without peeling or flaking. Ideal for high-performance parts, it extends component life while maintaining a flawless finish.
Compared to traditional metal plating, PVD allows for the deposition of a wide variety of inorganic coating materials across an extensive range of substrates. With multiple PVD techniques available, manufacturers can achieve diverse finishes tailored to suit nearly any component or application.
Application of PVD Coating
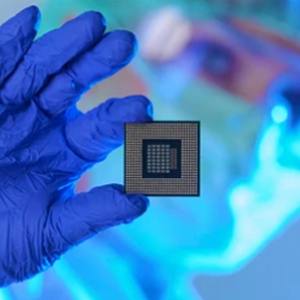
Microelectronics
Thin films are applied to electronics like phones and circuits to boost conductivity, durability, and device performance, even enabling superconductive properties in some cases.
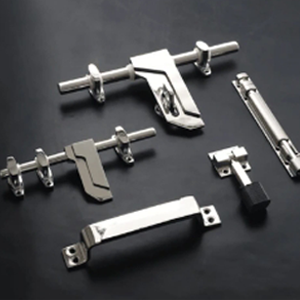
Home Hardware
Home fixtures like taps, sinks, and handles often use vacuum coatings, such as nickel, stainless steel, copper, bronze, or black PVD, for added durability and style.
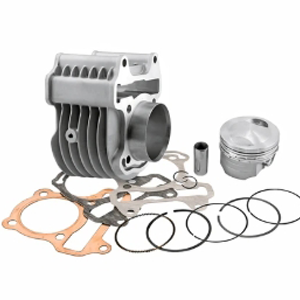
Automotive Applications
Automotive parts like trim, engine components, and headlamps often use chrome coatings. PVD offers a cleaner, more durable alternative to traditional electroplating.
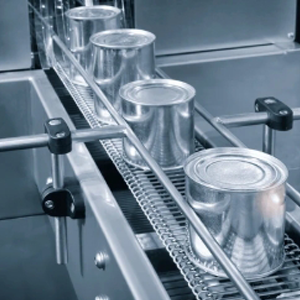
Food Packaging
Aluminum is common in food packaging, but its rigidity limits use. Aluminum-coated plastic is widely used for snacks to keep them fresh.
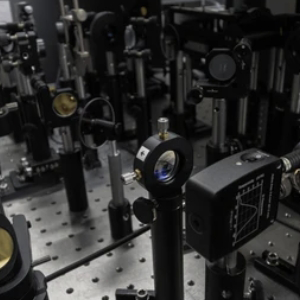
Optics
PVD coatings enhance plastic lenses, car windows, and research materials by adding scratch resistance, UV protection, and durability—without compromising clarity.
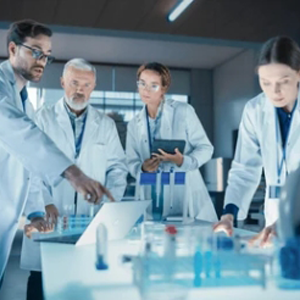
Medicine
Creates a tough, protective coating, ensuring superior corrosion resistance and longevity for each component.
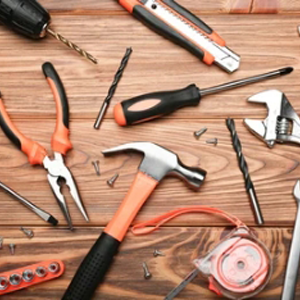
Home Tools
Stainless steel tools often use hard PVD coatings like titanium nitride or DLC to stay sharper longer, crucial for high-pressure applications like drilling.
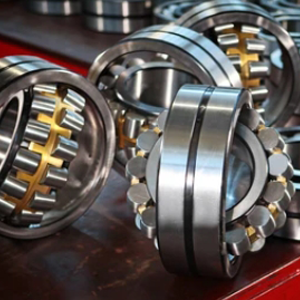
Decorative Applications
PVD offers diverse colors and finishes for decorative use on materials like copper, nickel, chrome, or ceramics. It outperforms traditional metal finishing in hardness and fade resistance.
Our Facilities
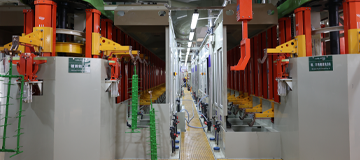
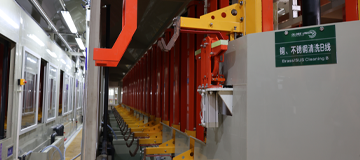
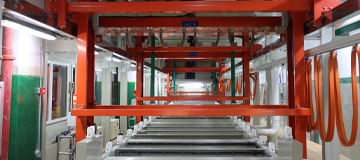
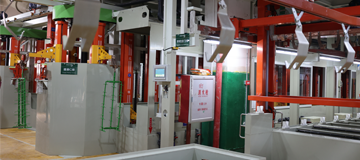
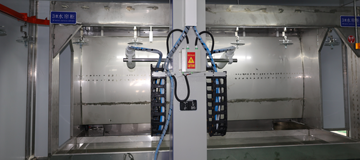
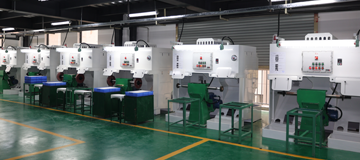
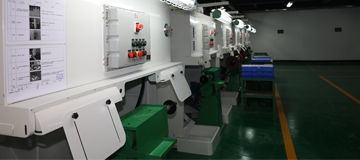
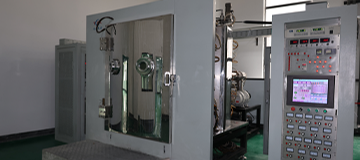